I was tired struggling with crappy Buell engine unsuccessfully trying to seal the throttle body to cylinder head interface. So I decided to try different way and to design my own intake manifold flanges. This idea was inspired by this product https://www.twinmotorcycles.nl/artikelen.asp?cid=7&aid=189 designed and successfully tested by Twin Motorcycles. But the issue is those flanges are for old Buell XB and do not fit the new 2008-2010 Buell XB and there is no similar product on the market for newer Buell XB. And so on here my project has started.
The main problem here is how to improve the sealing interface between manifold intake and cylinder head when you have very limited space around those sealing area. The guys from Twin Motorcycled decided to use two o-rings instead of one thick sealing ring, so you can make the flange slightly thicker and wider and increase rigidity of the flange. This design also allows to separate lateral force to clamp the seal to the cylinder head face from the force to squeeze the seal around the manifold intake tube so you need less force to seal the flange and as result there is less flange deformation.
I carefully measured the throttle body and cylinder head intake area and created CAD model. Then I figured out that I can slightly increase the flange thickness and make it slightly wider and also optimize the flange structure with more available space using o-rings.
Here is the new flange
Here is section view of original flange vs new flange
Another thing I decided to improve is material. It seems to me the original flange metal is not stiff enough. So I decided to make the new flanges out of strongest aerospace grade 17-4 PH stainless steel.
Here is the flange drawing
And here are my hight performance flanges
O-ring material is Viton with hardness 75A. I ordered them on McMaster. O-rings set for both flanges costs less than one set of James Gaskets intake manifold seals.
Here are installed o-rings
Flanges work fine right after first installation, no leakage at all. Installation process is significantly easier than installation of original flanges and gaskets. Later I will have more feedback after more miles on them.
High performance flange CAD model and drawing you can download here and build your own parts https://drive.google.com/file/d/1vF8v4Zr-2_sdBrUI6FePkD5mI0qZJnQI/view?usp=sharing
I recommend you to use 17-4 PH stainless steel for the flanges.
Standard size Viton gaskets you can buy on McMAster. You need two sizes o-ring for tube seal and for flange seal:
-Chemical-Resistant Viton® Fluoroelastomer O-Ring Super-Resilient, 3/32 Fractional Width, Dash No.135 https://www.mcmaster.com/#1288n229/=1abgg37
-Chemical-Resistant Viton® Fluoroelastomer O-Ring Super-Resilient, 3/32 Fractional Width, Dash No.133 https://www.mcmaster.com/#1288n227/=1abgg3y
I replaced the original flanges bolts by another longer bolts (since the flanges are thicker than original flanges) with flanges for better load distribution (Hex Head Screw, Flanged, 5/16"-18 Thread Size, 7/8" Long https://www.mcmaster.com/#92316a315/=1abgdar ).
The main problem here is how to improve the sealing interface between manifold intake and cylinder head when you have very limited space around those sealing area. The guys from Twin Motorcycled decided to use two o-rings instead of one thick sealing ring, so you can make the flange slightly thicker and wider and increase rigidity of the flange. This design also allows to separate lateral force to clamp the seal to the cylinder head face from the force to squeeze the seal around the manifold intake tube so you need less force to seal the flange and as result there is less flange deformation.
I carefully measured the throttle body and cylinder head intake area and created CAD model. Then I figured out that I can slightly increase the flange thickness and make it slightly wider and also optimize the flange structure with more available space using o-rings.
Here is the new flange
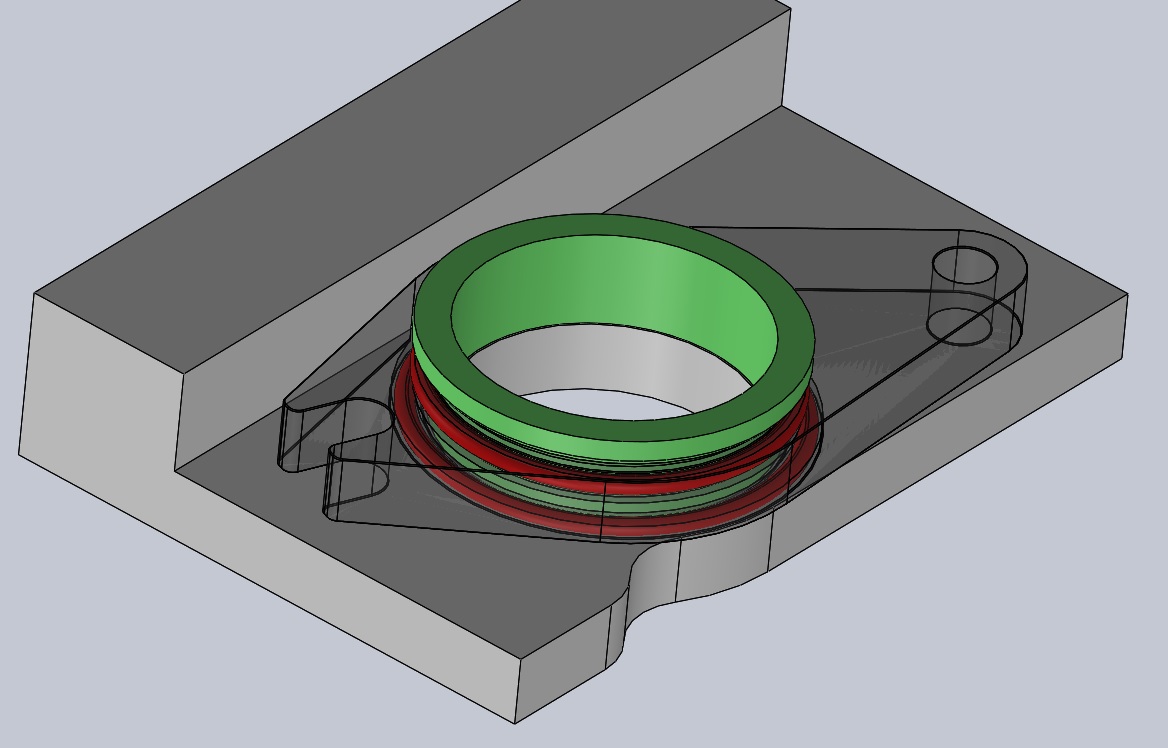
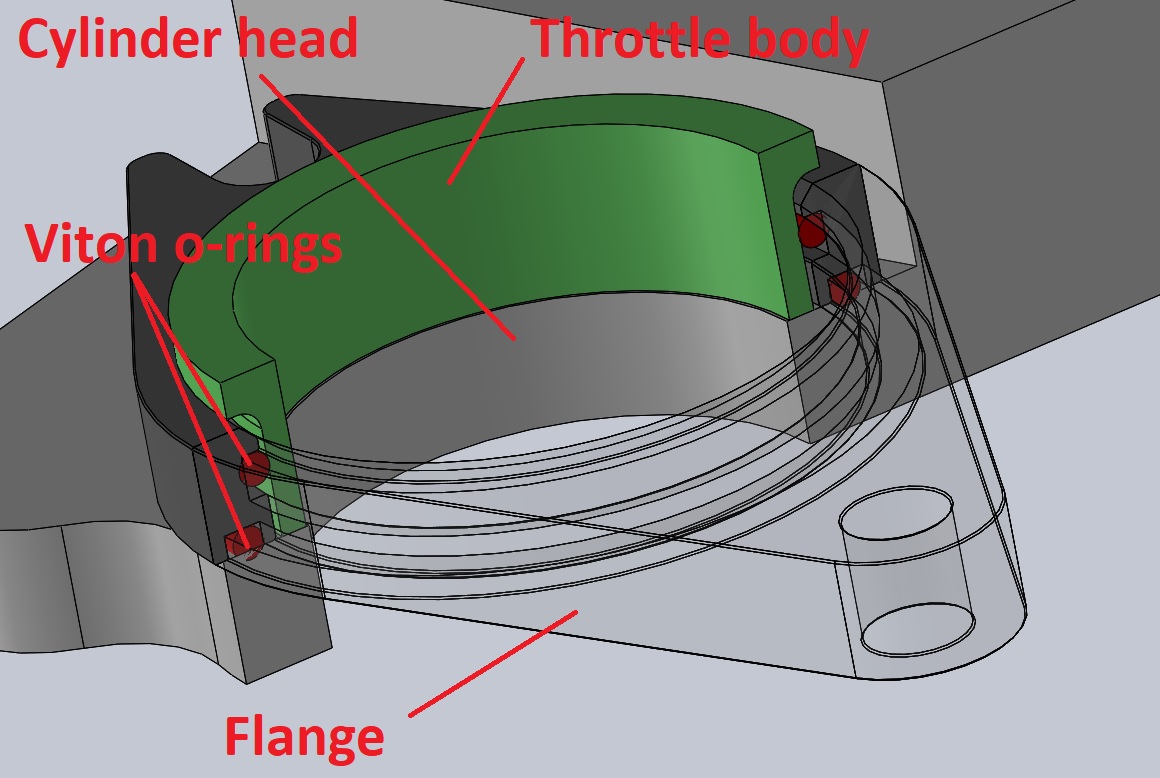
Here is section view of original flange vs new flange
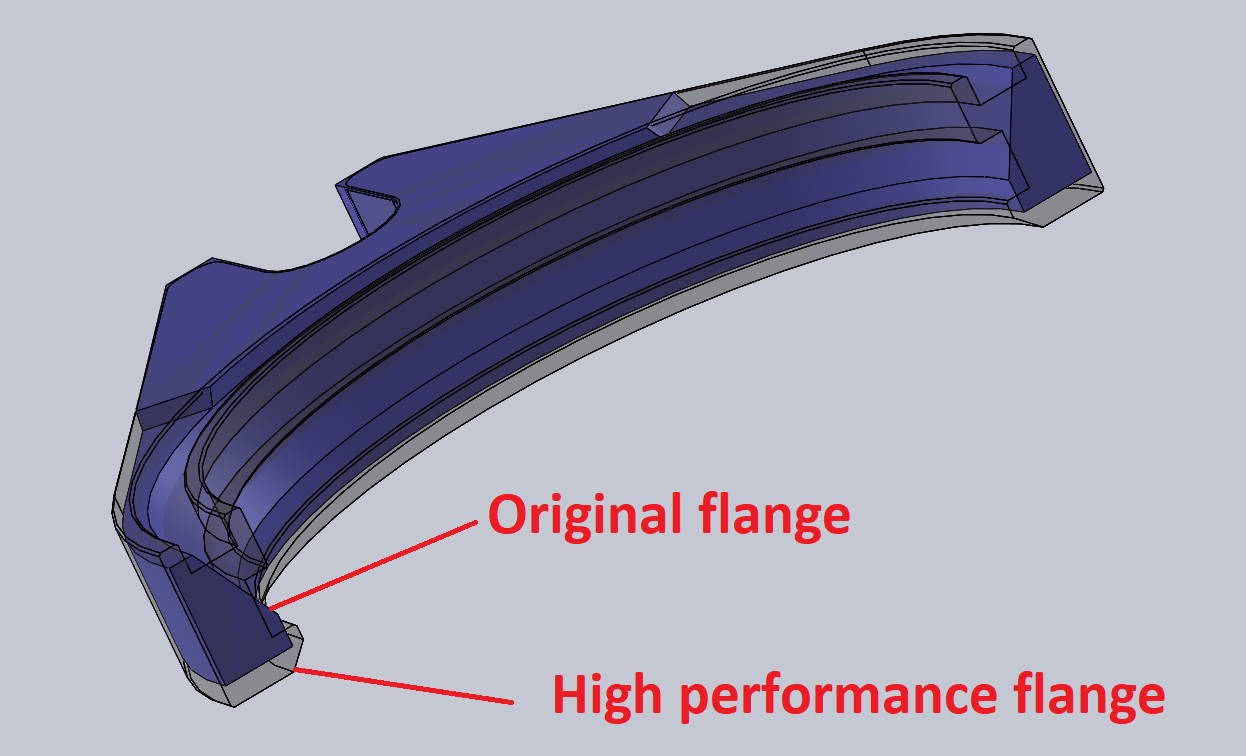
Another thing I decided to improve is material. It seems to me the original flange metal is not stiff enough. So I decided to make the new flanges out of strongest aerospace grade 17-4 PH stainless steel.
Here is the flange drawing
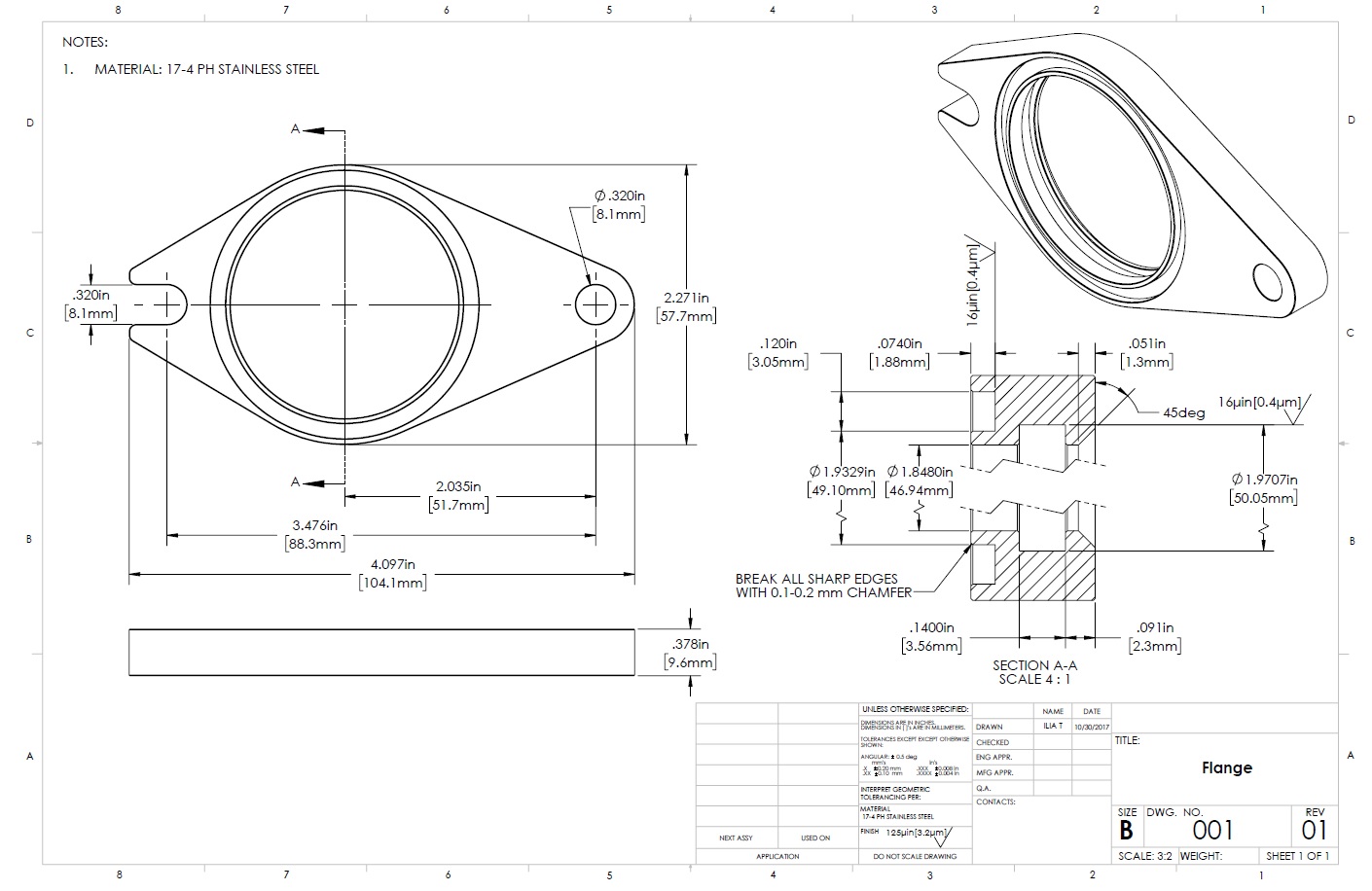
And here are my hight performance flanges

O-ring material is Viton with hardness 75A. I ordered them on McMaster. O-rings set for both flanges costs less than one set of James Gaskets intake manifold seals.
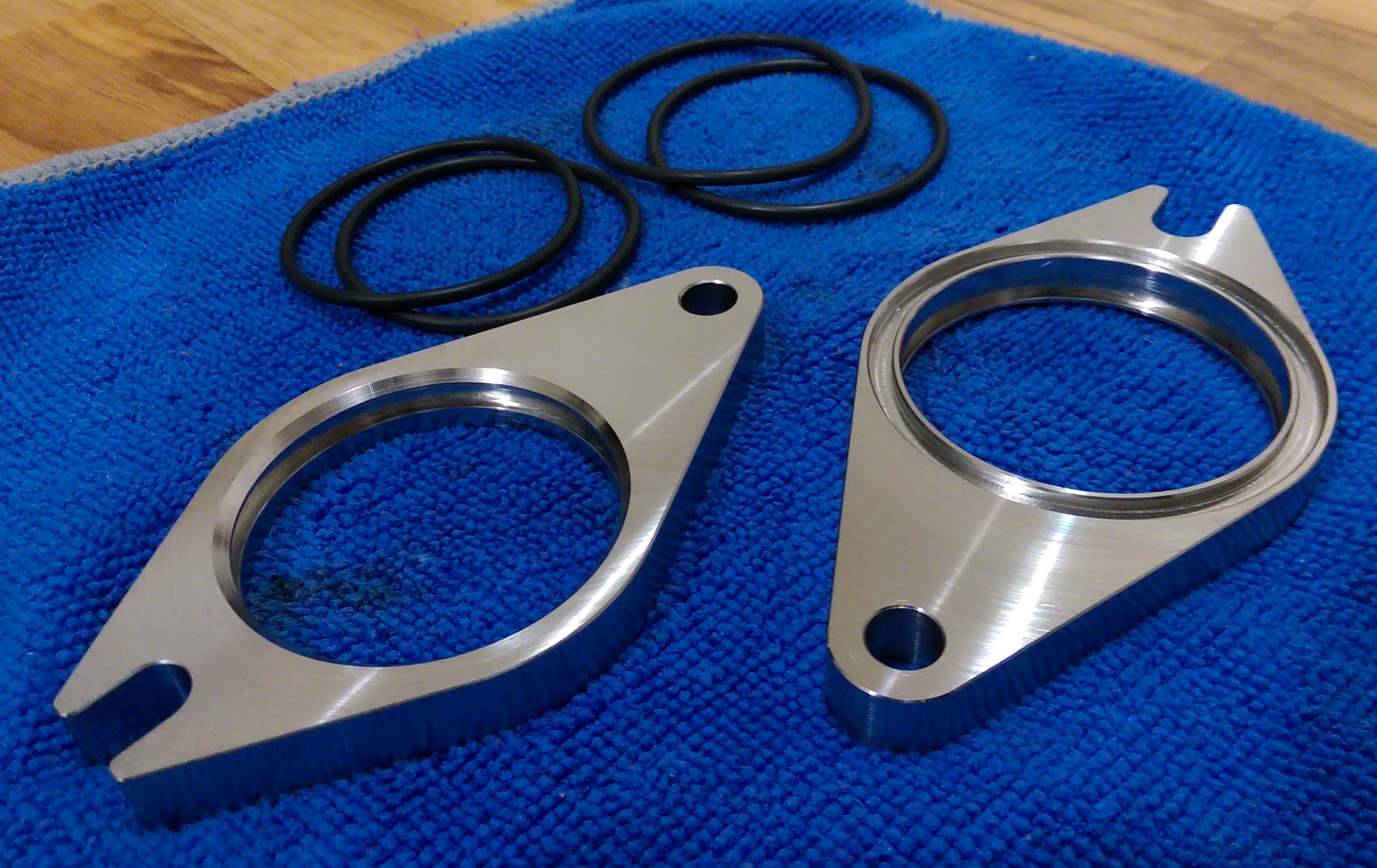
Here are installed o-rings
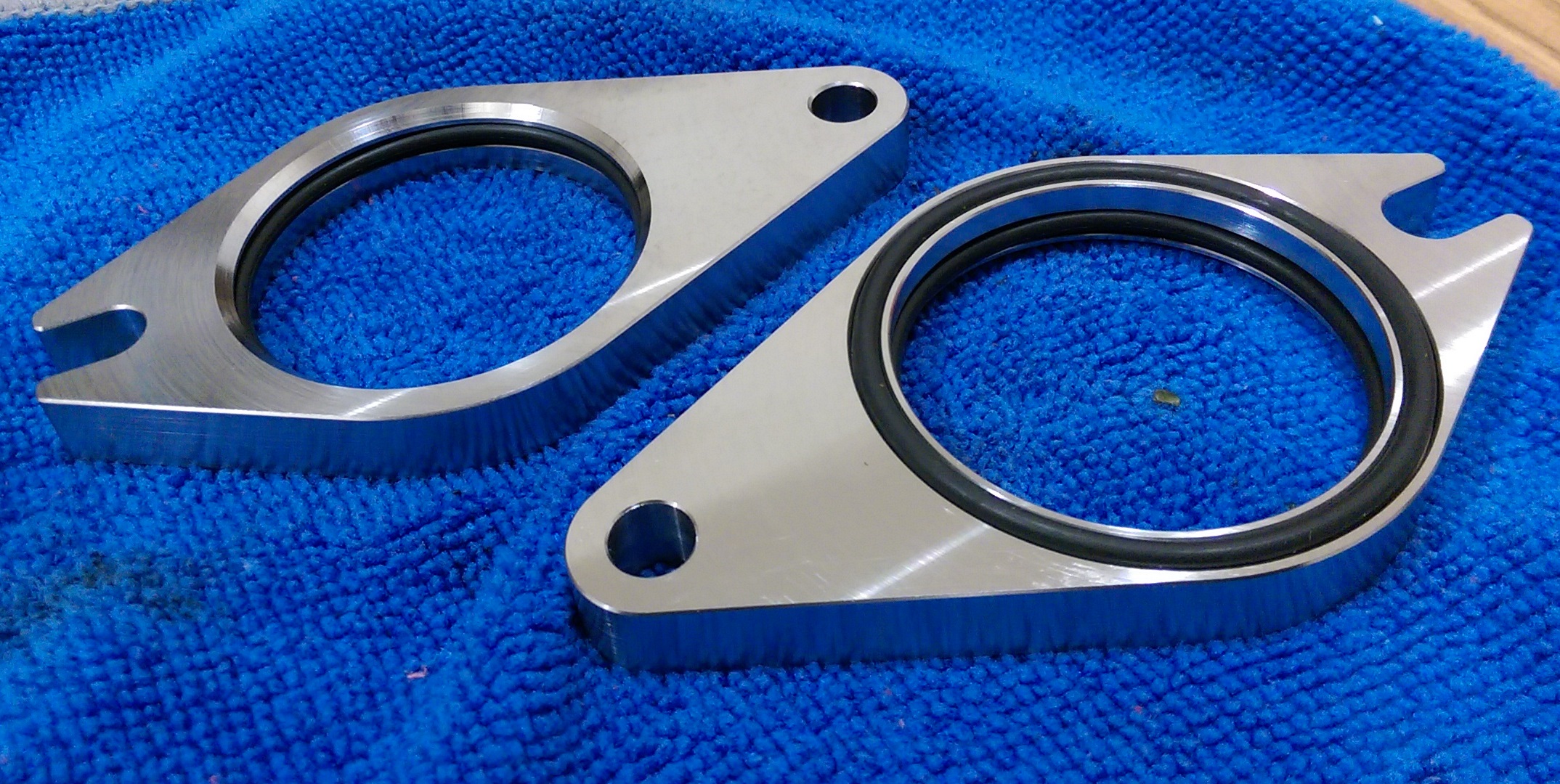
Flanges work fine right after first installation, no leakage at all. Installation process is significantly easier than installation of original flanges and gaskets. Later I will have more feedback after more miles on them.
High performance flange CAD model and drawing you can download here and build your own parts https://drive.google.com/file/d/1vF8v4Zr-2_sdBrUI6FePkD5mI0qZJnQI/view?usp=sharing
I recommend you to use 17-4 PH stainless steel for the flanges.
Standard size Viton gaskets you can buy on McMAster. You need two sizes o-ring for tube seal and for flange seal:
-Chemical-Resistant Viton® Fluoroelastomer O-Ring Super-Resilient, 3/32 Fractional Width, Dash No.135 https://www.mcmaster.com/#1288n229/=1abgg37
-Chemical-Resistant Viton® Fluoroelastomer O-Ring Super-Resilient, 3/32 Fractional Width, Dash No.133 https://www.mcmaster.com/#1288n227/=1abgg3y
I replaced the original flanges bolts by another longer bolts (since the flanges are thicker than original flanges) with flanges for better load distribution (Hex Head Screw, Flanged, 5/16"-18 Thread Size, 7/8" Long https://www.mcmaster.com/#92316a315/=1abgdar ).
Last edited: